Electrically Free Thermal Actuator for Precision Control
Athira Kattiparambil Sivaprasad — Hector RCD Jingyuan Xu
Non-electric actuators offer a promising alternative for sustainable and remote operations. My research focuses on the development of thermal micro-actuators based on thermomagnetic thin films, which harness the intrinsic material property of magnetization loss near the Curie temperature to achieve controlled mechanical motion. Unlike conventional actuators that rely on electrical stimulation, these devices operate by thermal triggering, eliminating the need for continuous electrical input and thereby reducing power consumption.
Magnetic shape memory alloys such as Heusler alloys, and ferromagnetic materials like lanthanum-iron-silicon alloys, are commonly classified as thermomagnetic materials (TM films). These materials exhibit changes in magnetization in response to variations in temperature and magnetic field, making them well-suited for self-actuating mechanisms in thermomagnetic systems.
The core working principle relies on the thermomagnetic effect: when heated above their Curie temperature (Tc), thermomagnetic materials lose their magnetization. This shift in magnetic properties can be harnessed to induce movement in a magnet, resulting in mechanical actuation as shown in Figure 1. The primary advantage of these actuators lies in their ability to operate without the need for external electrical input, utilizing ambient or waste heat as a power source, thus providing a highly sustainable approach to actuation. At miniature scales, the high surface-to-volume ratio facilitates faster heat transfer, enabling quicker actuation responses.
The project encompasses the design, microfabrication, and characterization of various actuator geometries, aiming for increased mechanical output (force and displacement), higher actuation frequencies, and improved thermal response times upon contact. By enhancing these key performance metrics, the project seeks to establish thermomagnetic actuators as viable candidates for integration into precision-dependent systems. These thermally driven high-force micro-actuators have significant application potential in advanced technologies, enabling compact, low-energy actuation for soft robotics, wireless motion control in biomedical tools, and precise thermal tuning in optical and photonic systems.
Figure 1. Operating principle of a thermomagnetic (TM) actuator: (A) When the TM material is below its Curie temperature (Tc), it becomes magnetized and is attracted toward a nearby permanent magnet due to the resulting magnetic force (Fm). Upon contact, the temperature of the TM material rises above Tc, resulting in a loss of magnetization; the restoring force (Fr) then returns the material to its original position. As it cools below Tc, magnetization is re-established, enabling a self-sustained actuation cycle (B) Magnetization vs. temperature curve illustrating the sharp magnetic transition of the TM material around Tc.
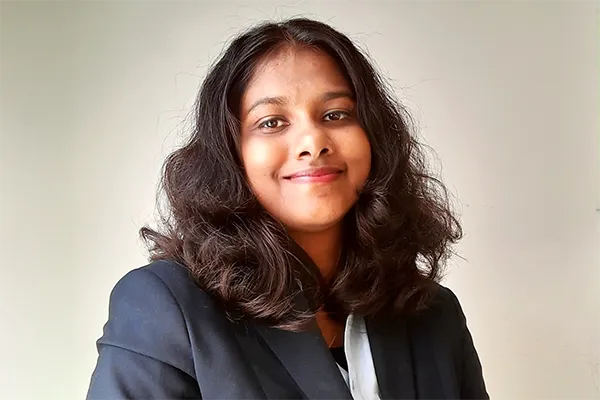
Athira Kattiparambil Sivaprasad
Karlsruhe Institute of Technology (KIT)Supervised by
Jingyuan Xu
Engineering, Energy & Material EngineeringHector RCD Awardee since 2023